compression test carbon fiber|A Closer Look at Composite Compression Test : convenience store ISO 14126 covers compression test methods, both shear and end loaded, for carbon fiber reinforced plastics and other composites. There are separate ASTM methods that cover those two modes of compression, ASTM . Resultado da 3 dias atrás · Their coach will be Ego Jinpachi, who intends to “destroy Japanese loser football” by introducing a radical new training regimen: isolate 300 young strikers in a prison-like institution called “Blue Lock” and put them through rigorous training aimed at creating “the world's greatest egotist .
{plog:ftitle_list}
WEBConseguiu? . ruyva.reels2 · Original audio

Compression test of a single carbon fiber in a scanning electron
Compression testing of composites can be a minefield. With countless different standards based on three different means of load introduction, many fixture variations and a . ISO 14126 covers compression test methods, both shear and end loaded, for carbon fiber reinforced plastics and other composites. There are separate ASTM methods that cover those two modes of compression, ASTM . A longitudinal compression test for a single polyacrylonitrile-based carbon fiber (T300) was performed using a scanning electron microscope. The compressive stress/strain . The tests were done in fully reversed loading of carbon-fiber reinforced epoxy laminates with different layups. The results show that for some layups, there is an influence of anti-buckling support design and fatigue life as .
The axial modulus of the fiber is the data of Toray T800 carbon fiber obtained in the experiment [18]. Other properties were referenced from the transverse and shear modulus of T300 carbon fiber measured by Hiroaki Miyagawa et al.[19,20], because the data on the shear modulus and transverse modulus of T800 carbon fiber is still not available. The carbon fiber reinforced Kagome-core sandwich panels were assembled with bonded laminate skins by Fan et al. [14]. It has been revealed that debonding would be the main weakness of the carbon fiber reinforced composite . Flatwise compression test was performed at a rate of 0.5 . Structural design and compression-bending test of ultra-lightweight carbon-fiber-reinforced polymer truss structures. Author links open overlay panel Shiping Li a b, Wujun Chen a b, Jianhui Hu a, . The carbon fiber prepreg used for the chord is T800, with a thickness of 0.1 mm, and the ply layers are arranged as follows: [45° /0° /0° /0 .
A longitudinal compression test for a single polyacrylonitrile-based carbon fiber (T300) was performed using a scanning electron microscope. The compressive stress/strain behavior was initially .The worldwide carbon fiber market was expected to be worth .7 billion in 2012, with an annual growth rate of 10%–12% from 2012 to 2018 (Das et al., 2016). Carbon fiber is used mostly in the automotive, aircraft, and energy industries thanks to its outstanding properties, given the fact that it is highly expensive to implement (Park, 2015 . For the three-point bending test, similar to the compression test, non-stitched, 12 k and 24 k carbon fiber stitched samples were tested. For each type of sample, the bending tests were also repeated 5 times to ensure the repeatability of the test results.COMPARISON OF OPEN-HOLE COMPRESSION STRENGTH AND COMPRESSION AFTER IMPACT STRENGTH ON CARBON FIBER/EPOXY LAMINATES FOR THE ARES I COMPOSITE INTERSTAGE 1. INTRODUCTION Mechanical testing of representative subelements of the Ares I composite interstage was per-formed as part of the development of .
This paper studied, for the first time, the effect of a crack parallel compression on the global Mode I fracture behavior of a carbon fiber polymeric matrix composite. To achieve this goal, an avant-garde experimental technique, originally coined elsewhere as The Gap Test, was designed, developed, and its nuances thoroughly documented for . A cyclic compression test revealed that the T300 carbon fiber deformed elastically up to ∼90% compressive strength. The variability in the compressive strength was evaluated using Weibull analysis. Hamada et al. [35] conducted a test on carbon/epoxy and carbon/PEEK and the final result shows that the 0 ° carbon fiber/PEEK has the highest value. Mael Arhant et al. [38] designed, manufactured and tested thermoplastic composite pressure vessels based on the consideration of technology, economics and ecology.
This Test Bench focuses on a very special new Eminence product, the new N314X 1.4" compression driver. The N314X is the first compression driver that uses TeXtreme composite for a diaphragm. TeXtreme thin-ply carbon is a novel type of material that is used in applications that require a high degree of stiffness performance in combination with ultralight . In the present study the properties of carbon fiber reinforced poly ether ketone (PEK) is compared with carbon fiber reinforced epoxy (EP) composite fabricated by compression moulding technique .
Carbon Fiber Reinforced Polymer (CFRP) composites, known for its high specific strength and stiffness ratio as well as design flexibility, . The quasi-static compression test aims to investigate the influence of hygrothermal environment by comparing the mechanical performance of specimens before and after aging. This investigation provides a .
Hollow struts from carbon fiber reinforced polymer (CFRP) were used for construction of octet lattice structure. With the help of a quasi-static compression test, the compressive modulus and strength of the studied octet lattice systems with different relative densities (0.85%, 1.33% and 2.17%) were calculated.
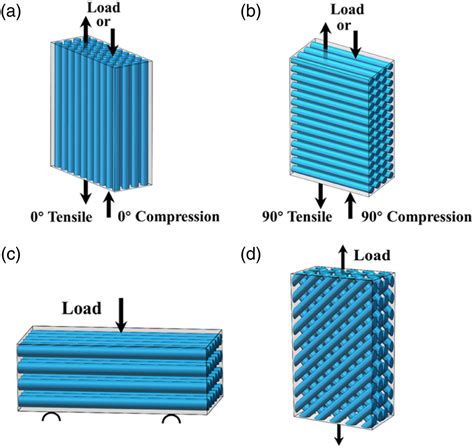
Tensile tests were carried out on carbon fiber high-entropy alloy, carbon fiber aluminum alloy, carbon fiber titanium alloy, and carbon fiber-reinforced composite laminates. Their mechanical properties were investigated at the tensile strain rates of 3
Structural design and axial compression test of novel carbon-fiber-reinforced polymer truss supporting rear connection-ring. Author links open overlay panel Shiping Li a b, Wujun . The CFRP truss is composed of two parts: chords and the web. The carbon fiber prepreg used for the chord is T800, the thickness of each layer is 0.1 mm, and the . CFRPs generally have very complex failure mechanisms, and their material properties are uncertain owing to their manufacturing process. 9,10 Numerous certification tests have been established in light of such . Bos et al. found that flax fiber has a high compression-to-tensile ratio of 80% in the loop test. Meng et al. found the average ratio of tensile to compressive modulus is 0.9 due to misalignment of fiber and production problems (porosity content). In addition, the inclination angle of fiber was measured using an indirect method and the . Compression-After-Impact analysis of carbon fiber reinforced composite laminate with different ply orientation sequences. Author links open overlay panel Vaibhav Somaji Anuse a, K. Shankar a, . are subjected to a compression test in a servo-controlled hydraulic compression testing machine of a capacity of 400KN, which gives the CAI strength .
The compression experiment was conducted according to the standard GB/T 1448-2005 (test method for compression properties of fiber-reinforced plastics). The loading speed was 2 mm/min. The test was carried out under the conditions of one atmosphere pressure and a constant temperature of 25 °C.
Compression properties of carbon fiber
Carbon fiber reinforced plastic and reinforced polymers are gaining importance as light-weight material. There are various disciplines for material testing that especially apply to carbon fiber materials. Most common are destructive tests, such as stress, fatigue and micro sectioning tests. There are also methods that allow non-destructive testing (NDT), so the material can be still . It's also worth noting that the pipes are weighed prior to the test. As you might expect, acrylic is the lightest at 9 grams, with PVC and carbon fiber tied at 11 g.
EXPERIMENTAL PROGRAM The present experimental program was designed to investigate the compression and flexure test on carbon nanotubes concrete modified with carbon and polypropylene fiber integrated with High performance concrete (HPC) of grade M60, It consists of casting and testing of cubes and prisms specimens of five concrete matrices (i . 1. Introduction. Compression testing is not a trivial task in continuous high strength and high modulus fiber reinforced polymer composites. The compression test of a composite specimen can be considered a structural test having complex interactions between local failures and structural instabilities [1].In the compression test, several failure mechanisms can occur . Longitudinal direct compression test of a single carbon fiber in a scanning electron microscope. Compos A Appl Sci Manuf (2014) J. Wang et al. Anisotropic compressive behaviour of turbostratic graphite in carbon fibre. Appl Mater Today (2017) S. Nunna et al. This paper describes axial compression test results of 27 concrete cylinders confined by carbon fiber reinforced polymer composite jackets. The experimental parameters include plain concrete compressive strength and the thickness of the composite jacket. .
A longitudinal compression test for a single polyacrylonitrile-based carbon fiber (T300) was performed using a scanning electron microscope. The compressive stress/strain behavior was initially .
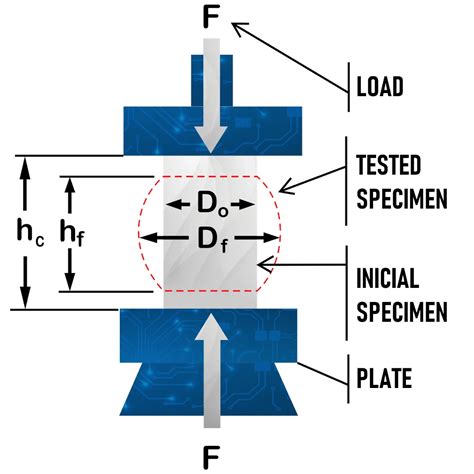
runnig compression test
WEBEnvie-nos uma mensagem, vamos responder o mais rápido possível. O Grupo Fatal Model é uma companhia brasileira de tecnologia e serviços de internet, proprietária das .
compression test carbon fiber|A Closer Look at Composite Compression Test